The ultimate guide to managing aircraft teardowns end-to-end
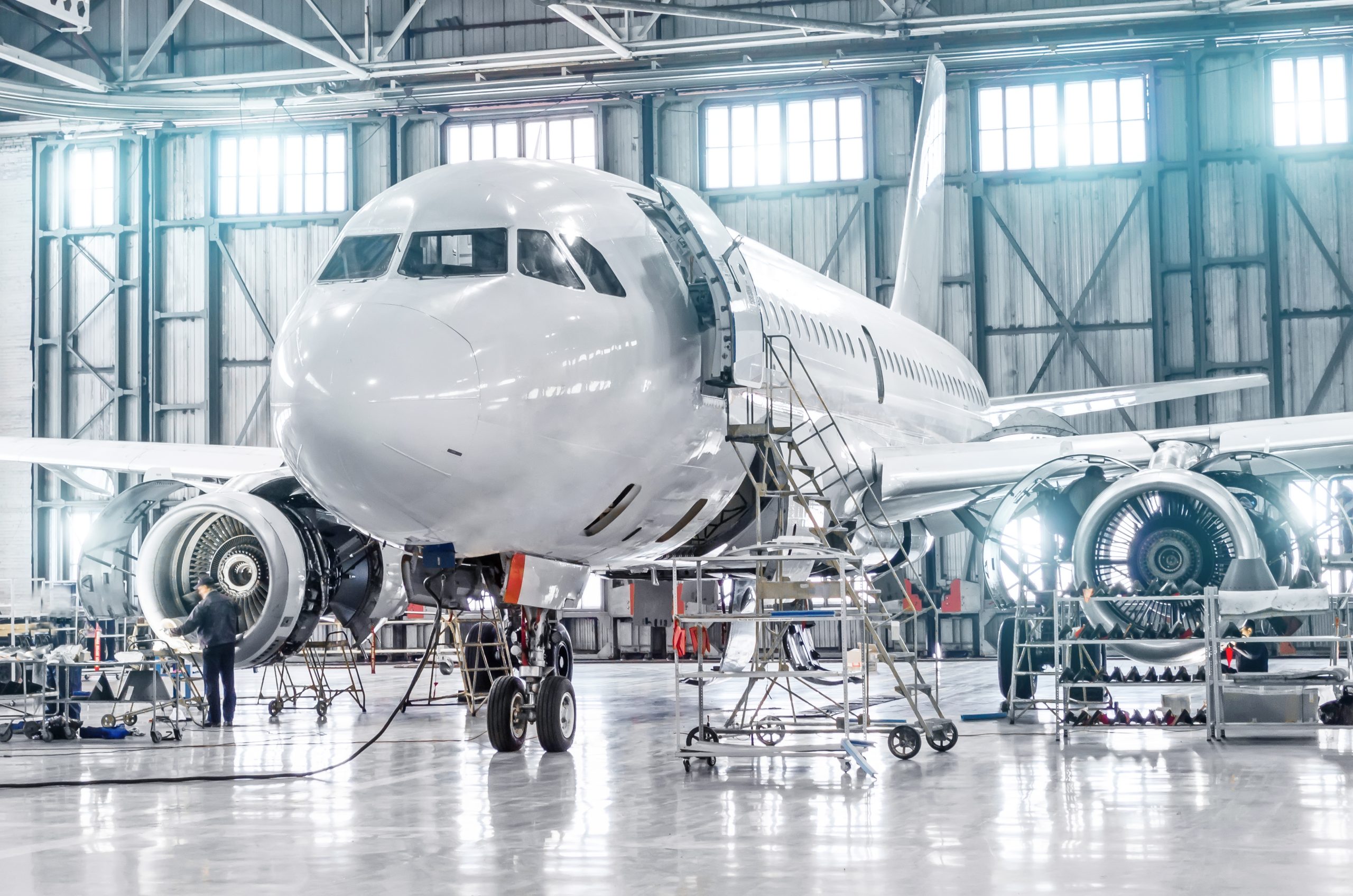
Aircraft industry estimates suggest that globally around 800 to 1,000 aircrafts are retired annually, with many undergoing teardowns every year. From an aircraft`s first take-off to its final landing, it serves as a vital component of the aviation industry and when it reaches the end of its service life, the process of teardown begins—a methodical and highly regulated operation to recover valuable components, recycle materials, and maximise returns. At XS Aviation, we specialise in managing this complex journey, ensuring every step is smooth, compliant, and profitable.
Here’s how we take care of every detail in an aircraft teardown.
A Teardown Begins with Planning
It all starts with understanding the purpose of the teardown. Is the goal to recover valuable parts for resale, recycle materials for sustainability, or both? Each project begins with a thorough assessment of the aircraft. We evaluate its model, age, maintenance history, and condition, analysing which components have the most value in the current market.
Regulatory compliance is key at this stage. Aviation authorities like the CAA, FAA, and EASA require meticulous documentation, including airworthiness certificates and traceability records for each part. Selecting the right teardown facility is also critical; it must have the necessary certifications and environmental safeguards to ensure a successful operation.
Coordinating Key Players
Aircraft teardowns are not a one-team operation. They involve a network of specialists:
- Teardown experts to handle disassembly and inventory.
- Parts distributors to facilitate the resale of salvaged components.
- Recycling partners for unserviceable parts and materials.
Through careful coordination with these stakeholders, we ensure that all legal agreements, liability terms, and logistics are in place before work begins.
Preparing the Aircraft
Before the aircraft can be disassembled, it must be decommissioned and prepared. This includes draining all fluids, isolating electrical systems, and removing hazardous materials like fire extinguishers and oxygen tanks. A detailed inspection follows, during which every part is assessed for its condition and value. This inventory forms the backbone of the entire teardown process.
The teardown begins with the careful removal of high-value components such as engines, avionics, and landing gear. Each part is labelled, categorised, and stored properly to prevent damage or loss. Components are then segregated into serviceable and unserviceable categories.
- Serviceable parts are sent for repair and certification, ensuring they meet safety standards.
- Unserviceable parts are prepared for recycling or disposal, adhering to environmental regulations.
Documentation at this stage is critical. Every part is cross-checked with original records to maintain complete traceability, a requirement for resale and reuse in the aviation industry.
Adding Value Through Repair and Certification
Serviceable parts are sent to approved repair stations for inspection and refurbishment. Once restored, they are certified by aviation authorities with documentation like CAA Form 1, 8130-3, or EASA Form 1, depending on the region. These certifications guarantee the safety and quality of parts, increasing their value in the market.
Maximising Returns
Once the parts are certified, the focus moves to sales. Market trends are carefully analysed to identify demand for specific components, and connections are established with airlines, MROs, and distributors to match these parts with the right buyers. Whether it’s through direct sales, online marketplaces, or auction platforms, we ensure the value of every recovered component is fully maximised.
Recovered parts often require maintenance or repairs before returning to service:
- Repair Solutions – Parts are inspected and repaired at authorised facilities.
- Certification – After refurbishment, components receive EASA Form 1 or FAA 8130-3 approvals.
- Market Readiness – Certified parts are listed on recognised platforms (e.g., ILS, PartsBase) or sold directly through our Trading Services.
Additionally, we take care of all logistics, from secure packaging and efficient shipping to seamless customs clearance, ensuring the parts reach their destinations quickly and reliably, anywhere in the world.
Recycling for a Sustainable Future
For parts that can’t be reused, recycling is the next step. Materials like aluminium and composites are sent to specialised facilities, while hazardous waste is disposed of responsibly. This commitment to sustainability is a cornerstone of our approach, aligning with global efforts to reduce the aviation industry’s environmental footprint.
Responsible recycling aligns with today’s sustainability targets and can benefit operators pursuing eco-friendly practices. For more on the shift towards environmentally responsible aviation, see our case study on Transitioning to sustainable aviation.
Wrapping Up: Documentation and Insights
As the teardown concludes, we provide detailed reports documenting every activity, from parts recovered to waste recycled. Financial reconciliation ensures that all revenues and costs are accounted for.
At XS Aviation, we manage aircraft teardowns with precision and care. Our structured approach ensures compliance with regulations, maximises financial returns, and supports sustainability goals. By trusting us with your teardown project, you gain a partner who handles every detail, so you can focus on your next opportunity.
Contact XS Aviation today to learn how we can make your aircraft teardown a smooth, profitable, and environmentally responsible process. Visit XS Aviation or call us to discuss your need.