Is warehouse space costing you more than you think?
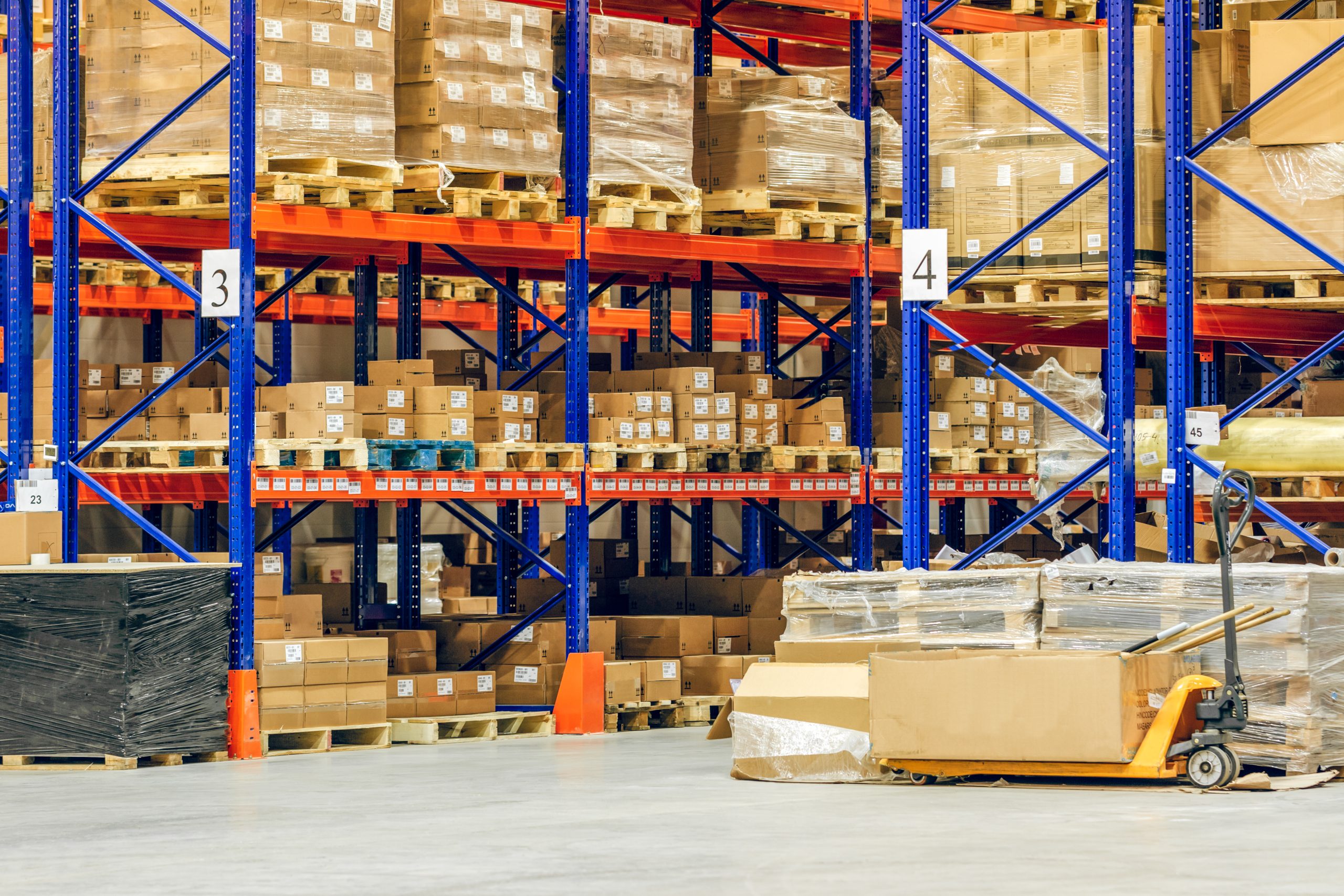
When it comes to the aviation industry, storage is not just about finding room for spare parts—it’s about safeguarding critical components that ensure the safety and functionality of aircraft. From tiny electronic chips to enormous structural elements, aircraft parts require careful handling and precise environmental control. Unlike traditional warehousing, which focuses primarily on volume and general conditions, aircraft surplus storage demands much more: strict adherence to safety regulations, climate control, and space optimisation. Failing to meet these standards doesn’t just cost money—it can lead to significant operational challenges.
The Unique Challenges of Aircraft Parts Storage
Aircraft spare parts are the backbone of any airline or maintenance organisation. Whether it’s a fragile electronic component or a massive turbine blade, each part plays a crucial role in keeping an aircraft operational and safe. But the challenge doesn’t stop at managing inventory. Many parts, particularly those for older aircraft, can become obsolete over time, leading to storage inefficiencies.
Consider aircraft electronic components, for instance, these parts are highly sensitive to environmental factors like humidity and static electricity. Without proper storage solutions—such as controlled environments and anti-static measures—there’s a high risk of damage, potentially making these costly components unusable. In this industry, improper storage doesn’t just mean a loss in product value—it could mean the failure of a vital aircraft system.
On top of that, larger components, such as structural elements, require careful space planning. You can’t just store these parts in any warehouse corner. They need ample room for handling equipment to avoid any physical damage. Even a minor dent could mean costly repairs or replacements. This means that space, in the aviation industry, is not a luxury—it’s a necessity.
Space Optimisation: Turning Cost Into Efficiency
Warehousing is more than just about fitting everything in; it’s about optimising space to ensure that every square inch is used effectively. With aircraft parts, space management becomes even more crucial due to the high value of stored items. Storing excess inventory can tie up significant capital, leading to a reduction in liquidity—cash that could otherwise be invested in more urgent or lucrative areas of the business.
Moreover, regulatory bodies like the Federal Aviation Administration (FAA) and European Union Aviation Safety Agency (EASA) have strict requirements on how aircraft parts should be stored. Dangerous goods, such as lithium batteries or chemicals, must be secured and placed under strict environmental controls, further complicating the warehouse layout. Failing to comply with these regulations could not only result in fines but also risk operational downtime if the necessary parts aren’t readily available.
A significant part of space optimisation also involves balancing inventory levels. The aviation industry often uses just-in-time (JIT) inventory management to reduce the risk of overstocking, yet there’s also a need for buffer stock to minimise aircraft downtime. This is where XS Aviation steps in with managing your inventory and provide a solution to your problem of managing your inventory effectively and producing cost effective solutions.
The Global Impact of Inefficient Space Usage
Aircraft are global assets, and the parts that keep them flying need to be readily available for distribution across the world. But the reality is that warehouse space is often limited. Downtime for an aircraft is extremely costly, with each minute of delay adding up to significant losses for airlines. Also, storage inefficiencies can lead to bottlenecks. Overstocked shelves may look productive, but in reality, they can lead to chaos—picking errors, shipping delays, and even safety hazards.
Additionally, for parts with long shelf lives, periodic inspections are required. These inspections further complicate storage because they require easy access to parts that might otherwise sit undisturbed for months or years. Hence XS Aviation provides Surplus Management of your spare parts striving to become the most trusted in the industry.
Additionally, obsolete inventory is another major issue that ties up valuable space in aviation warehouses. As aircraft models are retired or upgraded, the spare parts for those models may no longer be needed. Storing too much inventory can also drain cash flow, locking up capital that could be better spent on growth initiatives or operational improvements. Meanwhile, understocking critical parts risks aircraft downtime, leading to delays and potential loss of revenue.
Optimising Space to Maximise Profit
Warehouse space isn’t just about storing parts—it’s about strategic, efficient management that maximises profitability. A poorly organised warehouse can lead to higher labour costs, order-picking errors, and safety risks, ultimately costing far more than just the price of rent. On the other hand, a well-optimised warehouse ensures that critical components are stored properly, retrieved quickly, and distributed globally without delay.
By addressing these issues head-on and treating warehouse space as a valuable asset, aviation industries can not only reduce costs but also enhance their overall operational efficiency. In a world where time and safety are everything, every square foot of warehouse space truly is money.